University to ‘revolutionise’ digital manufacturing offering following £500,000 investment
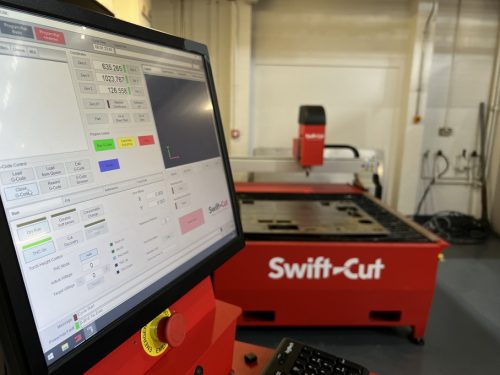
The University of Nottingham’s Faculty of Engineering has completed a major refurbishment project which will enable it to transform its digital manufacturing offering.
The university has invested half a million pounds in upgrades to its Rapid Prototyping (RP) and Engineering Applications (EA) workshops on University Park campus, improving the accessibility of both spaces and introducing a raft of new technologies for aspiring engineers to enjoy.
The extensive overhaul means students in the faculty can now get to grips with 50 3D printers, Fuse 1 SLS Machines, Stratasys F170 Fused Deposition Modelling (FDM) printers, a SwiftCut Pro plasma cutter and a range of Computer Numerical Control (CNC) machinery.
Simon Lawes, associate professor and course director for Mechanical Engineering, said: “While both facilities have existed for a long time, these upgrades will provide our mechanical and Product Design and Manufacturing students and researchers with brand-new facilities that will enable them to work in a faster, more sustainable way in an environment that mirrors those across the industry.
“As a centre for excellence in Additive Manufacturing, and home to one of the country’s biggest research groups, these new technologies provide researchers and students alike with a springboard to create more precise and complex designs, resulting in higher quality outputs that will really set them apart from others.”
Jason Young, technician in the Faculty of Engineering, added: “Technology is constantly evolving, which is why it’s crucial that we ensure our facilities are updated to reflect these advancements. The recent upgrade and refurbishment, along with the introduction of industry level automated machinery, offers our students the opportunity to enhance their design capabilities when producing physical components.
“Additionally, we now have a zonal workshop, which allows our students to have greater flexibility when it comes to producing manufacturing plans for project work, and have introduced offline programming solutions, allowing our students to simulate their designs for manufacture regarding material, tooling, and labour costs. All this combined means that our students now have the opportunity to produce parts with greater design freedom, while maintaining maximum efficacy, and all to an industrial level of accuracy and precision.”
The new facilities were officially opened earlier this month.